For automotive repair, MIG welding is your go-to process. It's widely used due to its speed, versatility, and ease of use. This method employs a continuous wire electrode, making it effective for various materials, including steel and aluminum. MIG produces clean welds, which means less post-welding cleanup for you. While TIG welding offers precision for delicate jobs, MIG remains the backbone of auto repair because of its efficiency and quality. If you're curious about other welding techniques and their applications, there's plenty more to discover about the art and science of automotive welding.
Key Takeaways
- MIG Welding is the most common method due to its speed, versatility, and clean welds for various materials like steel and aluminum.
- TIG Welding is preferred for precision repairs on thinner metals, ensuring high-quality welds, especially in exhaust systems.
- Stick Welding offers portability and effectiveness for outdoor applications, making it suitable for quick structural repairs on rusty surfaces.
- Flux-Cored Arc Welding (FCAW) is ideal for heavy-duty components, providing high welding speeds and flexibility in challenging environments.
- Each welding process requires specific tools and safety gear to ensure effective and safe automotive repairs.
Overview of Automotive Welding
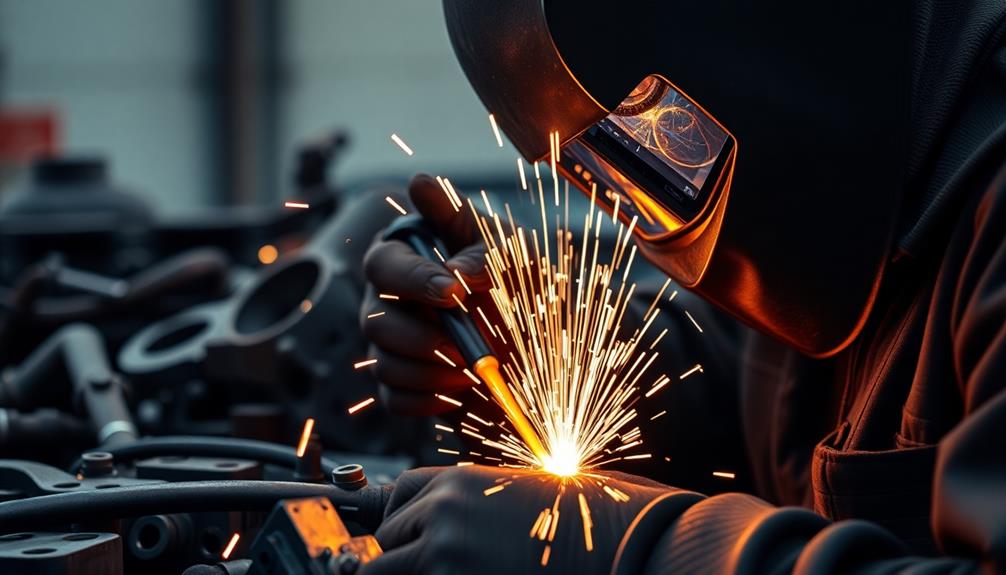
Automotive welding plays an essential role in both fabricating and repairing vehicle parts, ensuring that your car remains safe and structurally sound. When it comes to automotive applications, welding techniques like MIG and TIG are critical for achieving high-quality results.
MIG welding, known for its speed and versatility, is the go-to method for bodywork. It's particularly effective on thin metals, allowing for quick repairs and fabrications without compromising strength.
On the other hand, TIG welding offers precision that's hard to match. This technique is ideal for custom fabrications and important components where aesthetics matter. TIG produces cleaner welds, making it perfect for applications where appearance and strength are equally important.
To execute automotive welding tasks safely and effectively, having the right equipment is essential. You'll need a reliable MIG or TIG welder, along with proper safety gear to protect yourself from hazards.
Understanding the differences between these welding methods can greatly impact the quality of your repairs and fabrications, ultimately ensuring your vehicle remains in top condition.
Common Welding Techniques
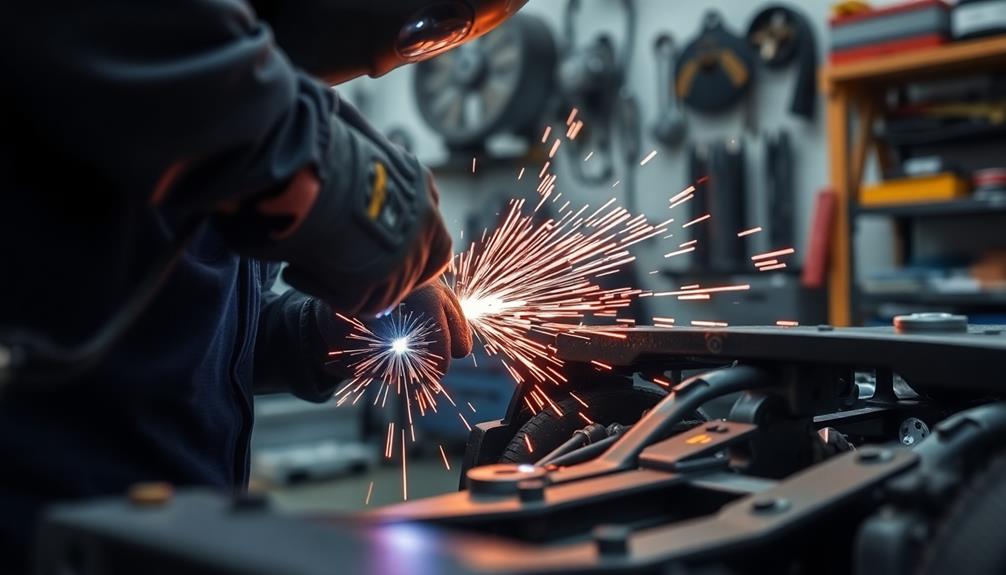
In the world of vehicle repair, understanding common welding techniques is key to achieving reliable and durable results.
MIG welding is the most widely utilized method in the automotive industry, prized for its speed and versatility in welding various metals. This makes it ideal for repairing body panels and structural components.
If you need precision and cleanliness, TIG welding is your go-to option. It's often used for intricate repairs and high-quality welds on critical components like suspension systems.
Another technique, stick welding, offers versatility for outdoor applications, effectively working on rusted surfaces. However, it's less common for aesthetic repairs in the automotive sector.
Spot welding is essential for automotive assembly, joining metal sheets at specific points to guarantee the structural integrity of body panels.
Finally, Flux-Cored Arc Welding (FCAW) is a portable option that delivers high welding speed, making it perfect for quick repairs in various outdoor settings.
Each of these welding techniques has its unique advantages, allowing you to choose the right one based on the specific needs of your vehicle repair project.
MIG Welding in Auto Repair
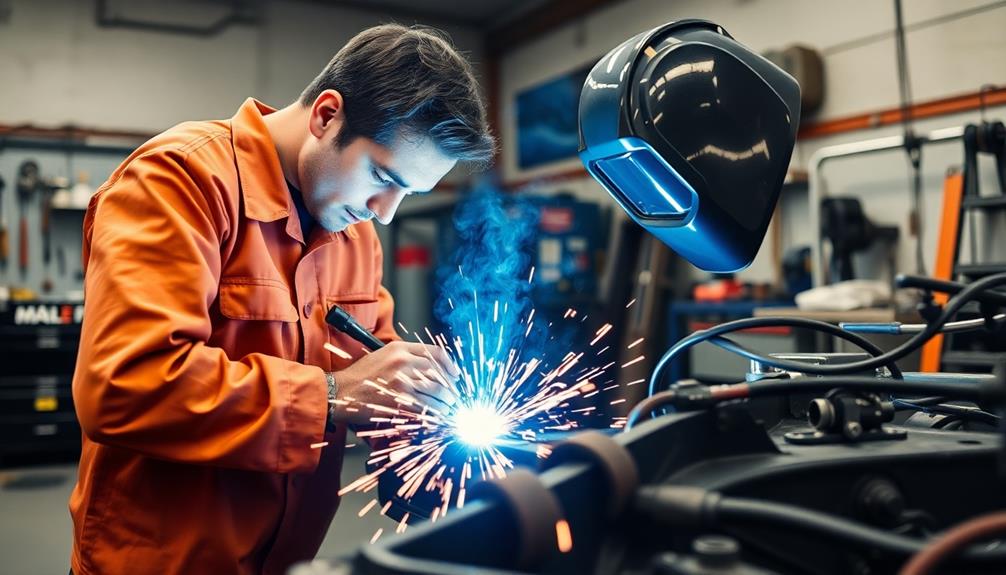
MIG welding, often referred to as the backbone of automotive repair, stands out for its speed and versatility. This technique, also known as Gas Metal Arc Welding (GMAW), uses a continuous wire electrode fed through a welding gun, creating an electric arc that fuses metal pieces together.
It's particularly favored in automotive settings for several reasons:
- It works well with various materials, including steel and aluminum.
- It produces clean welds with minimal post-welding cleanup.
- It's effective for both body panel repairs and structural components.
- Its efficiency helps reduce labor costs, making it accessible for both professionals and beginners.
With MIG welding, you get excellent control over the welding process, allowing for quick and aesthetically pleasing repairs. This is especially important for body panel repairs, where appearance matters.
The speed of MIG welding means less downtime for vehicles, which is a huge plus for any auto repair shop. By mastering this technique, you can streamline your work and deliver high-quality results that keep your customers satisfied.
TIG Welding Applications
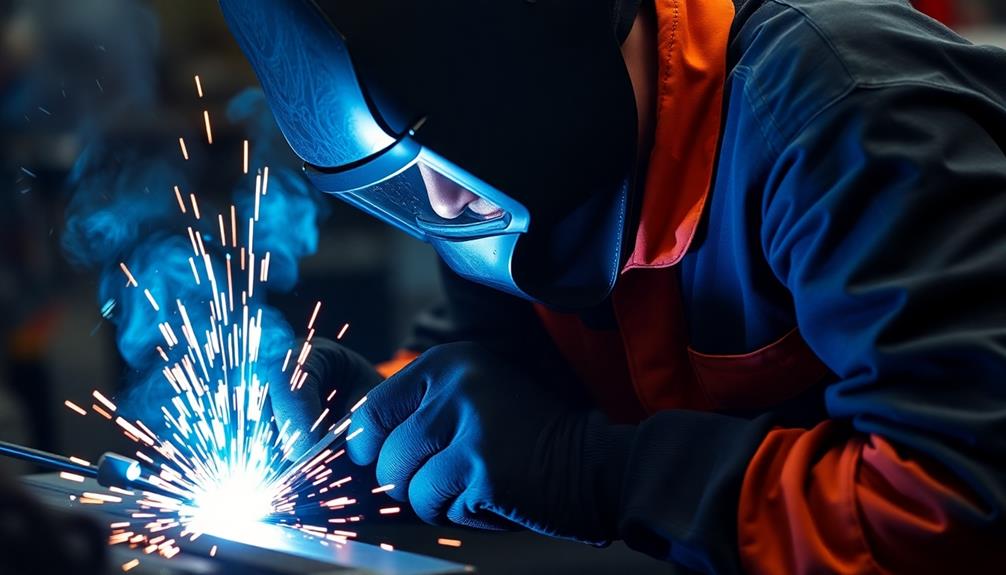
While MIG welding is popular for its speed and versatility, TIG welding offers unmatched precision for more delicate automotive repairs. This technique, known as Gas Tungsten Arc Welding (GTAW), is highly regarded in automotive applications for its ability to produce high-quality welds, especially on thinner metals like aluminum and stainless steel.
TIG welding utilizes a non-consumable tungsten electrode to generate an electric arc, allowing you to melt the base material with remarkable control. This level of precision is crucial for critical components such as suspension systems and custom fabrications, where both aesthetic appeal and structural integrity are essential.
One unique aspect of TIG welding is the manual feeding of a filler rod into the weld pool, enabling you to achieve intricate and detailed repairs that other methods can't provide.
Due to its cleanliness and precision, TIG welding is particularly favored for high-standard applications, including exhaust system repairs and vehicle restorations. If you're looking to guarantee quality and durability in your automotive repairs, TIG welding is certainly the process to evaluate.
Stick Welding Basics

Stick welding, or Shielded Metal Arc Welding (SMAW), is a reliable option for automotive repairs due to its portability and versatility. This technique uses a coated electrode to generate an electric arc, which creates a weld pool by melting both the electrode and the base metal.
You'll find that stick welding is particularly effective for outdoor applications and can handle rusty or dirty surfaces—perfect for many automotive repair situations.
Here are a few key points to evaluate:
- Portability: You can easily transport your equipment to various job sites.
- Versatility: It works well on different metals and conditions.
- Cost-Effective: Equipment is generally affordable and widely available.
- Skill Development: While it requires practice for clean results, mastering stick welding is rewarding.
Although stick welding isn't as precise as MIG or TIG welding, making it less ideal for aesthetic jobs, it excels in structural repairs.
The ability to create strong joints makes it a valuable choice in the automotive industry, especially when quick, reliable fixes are needed.
Flux-Cored Arc Welding
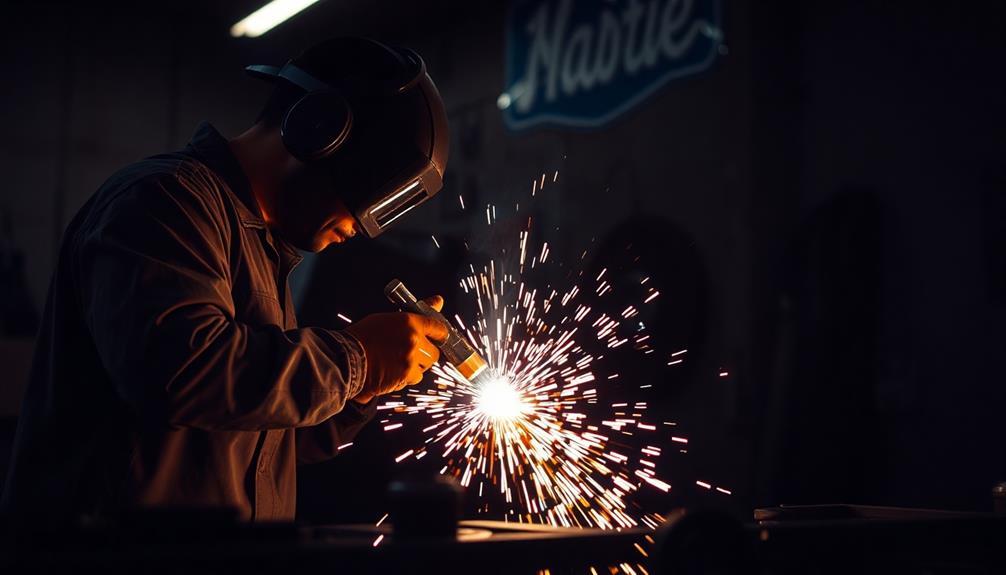
When it comes to automotive repair, Flux-Cored Arc Welding (FCAW) offers several advantages, like its ability to handle thicker materials and high welding speeds.
This makes it ideal for heavy-duty components such as frames and chassis.
You'll find that mastering FCAW not only enhances your skill set but also opens up a range of applications in the auto repair industry. Whether you’re tackling frame repairs, exhaust systems, or custom fabrication, FCAW (Flux-Cored Arc Welding) provides both versatility and strength. By combining this welding expertise with the best automotive repair software, you can streamline diagnostics, manage workflow efficiently, and ensure accurate cost estimates. Integrating technology with hands-on skills allows for smoother operations and higher-quality results in any automotive repair shop.
Advantages of FCAW
FCAW, or Flux-Cored Arc Welding, stands out for its impressive welding speed and adaptability, making it an excellent choice for automotive repair tasks.
This technique allows you to tackle various challenges with ease, especially in outdoor settings where conditions mightn't be ideal. Here are some advantages of FCAW that you should consider:
- High Welding Speed: You'll notice quick results, which is essential when time is of the essence in automotive repair.
- Flexibility: FCAW can be used with or without shielding gas, allowing you to adjust based on the materials and environment.
- Adaptability: You can manipulate variables like angle, voltage, and polarity, making it easier to meet specific welding requirements.
- Thicker Materials: While it may lack the precision of MIG and TIG methods, FCAW excels when working with thicker materials and various positions.
These features make FCAW a valuable asset in your automotive repair toolkit, especially when you need to balance speed and efficiency.
Just remember to use proper ventilation and protective gear due to the smoke and fumes generated during the process.
Applications in Auto Repair
In the world of automotive repair, the applications of Flux-Cored Arc Welding (FCAW) are numerous and impactful. This versatile welding process is often used for various auto body repairs, allowing you to tackle a wide range of tasks efficiently.
FCAW employs a tubular wire filled with flux, which not only protects the weld pool from contamination but also makes it effective for outdoor welding, where conditions mightn't be ideal.
One of the key advantages of FCAW is its ability to repair thick materials and even rusted surfaces, making it perfect for certain automotive maintenance scenarios. This capability means you can confidently address structural issues or panel replacements that require robust, durable welds.
However, it's important to keep in mind that the process generates significant smoke and fumes. Proper ventilation and protective gear are vital to guarantee safety while using FCAW.
By mastering this welding technique, you can enhance your skills as an aspiring auto body technician, providing you with the valuable capability to tackle diverse repair challenges in automotive welding.
Embrace FCAW, and you'll expand your toolkit for effective auto body repairs.
Essential Welding Tools

To achieve high-quality automotive repairs, you need the right welding tools at your disposal. The choice of welder, whether it's a MIG, TIG, or stick welder, depends on the specific application and materials you're working with. Each type has its advantages, so knowing which to use is essential for a successful repair.
Here are some important tools you'll need:
- Protective Gear: A welding helmet or goggles, gloves, and hearing protection are critical to safeguard yourself from harmful rays, burns, and noise.
- Clamps: These are essential for holding metal pieces in place during the welding process, guaranteeing precision and stability.
- Angle Grinder: Use this tool to prepare metal surfaces before welding and to smooth out welds afterward. It helps maintain quality and structural integrity.
- Welding Curtains: To create a safe work environment, these curtains prevent sparks and harmful UV light from affecting nearby workers.
Having these welding tools won't only enhance your efficiency but also guarantee that your automotive repairs are durable and safe.
Safety Considerations in Welding
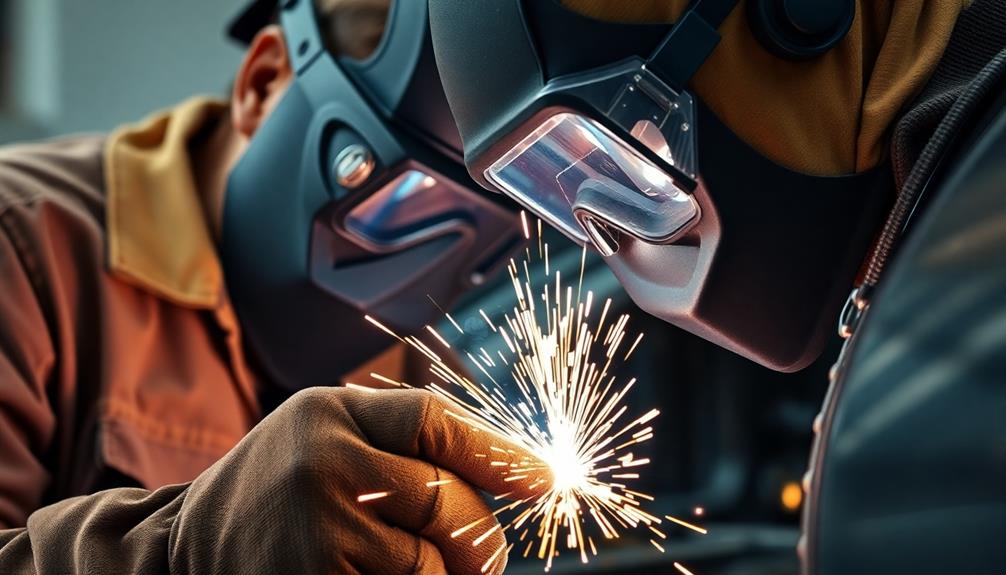
Welding safety is paramount for anyone working in automotive repair. You must prioritize safety considerations to protect yourself and others. Proper ventilation is essential to prevent inhaling harmful fumes and gases generated during welding. Additionally, don't forget your protective gear—wear welding helmets with appropriate shading, gloves, and fire-resistant clothing to safeguard against burns and eye injuries.
Here's a quick overview of key safety measures:
Safety Measure | Description |
---|---|
Protective Gear | Use helmets, gloves, and fire-resistant clothing |
Ventilation | Guarantee adequate airflow to disperse harmful fumes |
Electrical Hazards | Be aware of high voltages in welding equipment |
Shielding Gas | Prevent leaks to avoid health risks and explosions |
Awareness of electrical hazards is crucial since improper handling can lead to serious injuries. Furthermore, when using shielding gas, follow protocols to prevent leaks, which could create explosive environments. Always adhere to manufacturer repair guidelines and safety protocols, especially when dealing with vehicles that have sensitive electronics, to guarantee safe welding practices.
Benefits of Trade School Training

Trade school training in welding gives you the hands-on experience you need to thrive in the automotive repair industry.
With a focus on industry-relevant skills and techniques, you'll be well-prepared for various career advancement opportunities.
This practical training not only sharpens your abilities but also makes you a more attractive candidate to employers.
Hands-on Experience Opportunities
How can hands-on experience transform your welding skills in automotive repair? Trade schools provide a unique opportunity to engage with welding techniques like MIG, TIG, and spot welding in a controlled environment.
This practical training is essential for mastering the skills needed in the automotive repair industry.
Here are some benefits of hands-on experience in trade schools:
- Supervised Welding Sessions: You'll practice under the guidance of experienced instructors, receiving immediate feedback to improve your skills.
- Access to Industry-Standard Equipment: Working with high-quality tools prepares you for real-world challenges in automotive repair.
- Confidence Building: Engaging in hands-on exercises fosters your confidence and competence, ensuring you're ready for safety and precision in your work.
- Enhanced Employability: Employers often prioritize candidates who've practical experience, making your training an asset in the job market.
Career Advancement Potential
Gaining hands-on experience in welding not only sharpens your technical skills but also opens doors for career advancement. By enrolling in a trade school, you learn essential welding methods, including Metal Inert Gas (MIG) and Tungsten Inert Gas (TIG) welding, both vital for automotive repair.
As you develop these competencies, you position yourself as a valuable asset in the job market. Graduates from welding trade schools often find diverse opportunities as auto body technicians or in related fields like manufacturing and construction.
The structured training provided in programs like Combination Welding Technology equips you with the knowledge and skills necessary for entry-level jobs. Employers prioritize your practical experience and technical proficiency, making you more employable.
Moreover, skilled welders are in high demand, which translates to competitive salaries and significant potential for career advancement. As you gain experience and refine your welding techniques, you could also explore specialized roles or even supervisory positions within your workplace.
Ultimately, the investment in your welding education at a trade school can lead to a rewarding career with numerous growth opportunities.
Industry-Relevant Skills Development
Developing industry-relevant skills through trade school training is crucial for anyone aiming to excel in automotive repair. Trade schools provide hands-on experience with various welding techniques, including MIG and TIG, ensuring you're well-prepared for the demands of the automotive industry.
Programs like Combination Welding Technology offer structured training that equips you with the skills needed for entry-level jobs.
Here are some key benefits of trade school training:
- Hands-On Experience: You gain practical knowledge of welding techniques critical for automotive repair.
- Safety Protocols: You'll learn safety measures and equipment operation to minimize risks associated with welding tasks.
- Diverse Career Opportunities: Skilled welders are in high demand in the automotive repair and manufacturing sectors.
- Blueprint Interpretation: Understanding factory diagrams and blueprints is essential for effective automotive repair and fabrication.
Future Trends in Automotive Welding
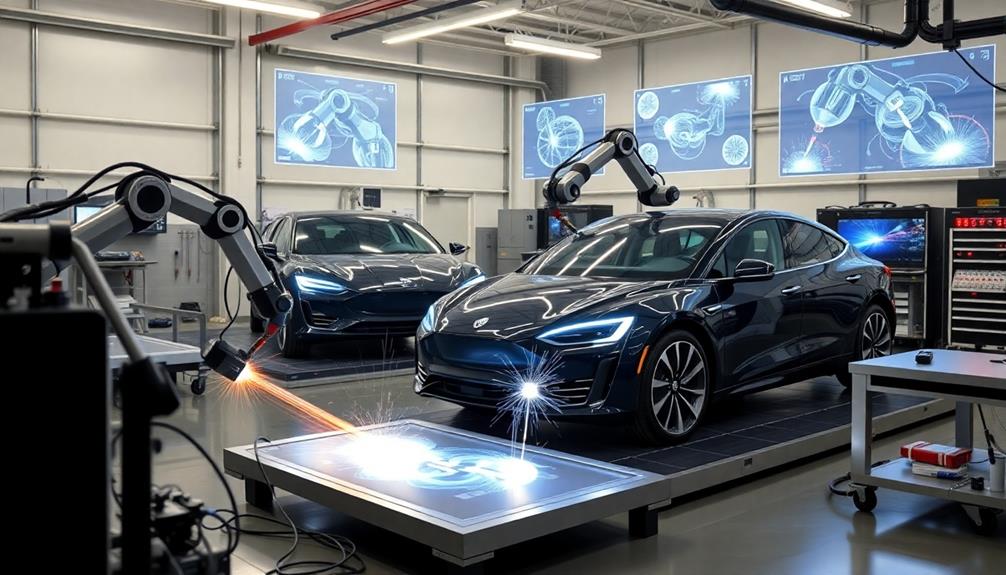
The future of automotive welding is poised for transformation, driven by advancements in automation and materials technology. You'll notice a notable shift as automation technologies, like robotic welding systems, enhance precision and efficiency in production and repairs. The rise of advanced materials, such as high-strength steel and aluminum alloys, will require specialized welding techniques to guarantee effective handling.
Innovations in welding technology, including laser and friction stir welding, promise stronger, lighter joints with minimized heat distortion. This is vital for modern vehicle performance. Additionally, the integration of smart welding machines equipped with real-time monitoring will improve weld quality and greatly reduce defects, addressing the growing demand for higher safety standards.
Lastly, sustainability trends are shaping the industry, leading to the development of environmentally friendly welding processes and materials. Here's a snapshot of these trends:
Trend | Description | Impact on Automotive Industry |
---|---|---|
Automation Technologies | Robotic systems for precision welding | Enhanced efficiency and consistency |
Advanced Materials | Use of high-strength steels and aluminum alloys | Need for specialized welding techniques |
Sustainability Trends | Eco-friendly processes and materials | Reduction in waste and energy use |
As the industry evolves, staying informed will be essential.
Frequently Asked Questions
What Process Is Automotive Repair Typically Done Using?
When you're considering automotive repair, you'll find that various welding processes are utilized. Each method has its unique advantages, tailored to different materials and repair needs, ensuring efficient and effective results for your vehicle's restoration.
Is MIG or TIG Better for Auto Body Work?
When deciding between MIG and TIG for auto body work, you'll find MIG's speed and ease make it better for most repairs. TIG excels in precision, but it's more suited for intricate, high-quality applications.
What Is the Best Welding Process for Auto Body?
Did you know over 70% of auto body shops prefer MIG welding for its speed and versatility? For your repairs, consider MIG for efficiency, but don't overlook TIG for precision work on critical components.
What Type of Welder Is Most Commonly Used in a Collision Repair Facility?
In a collision repair facility, you'll find MIG welders are the most commonly used. They're efficient and versatile, making quick work of repairs on thin metals, producing clean welds with minimal cleanup.
Conclusion
In the world of automotive repair, mastering welding processes like MIG, TIG, and stick welding can elevate your skills and expand your opportunities. Embracing safety precautions guarantees you work smart, while investing in trade school training sharpens your expertise. As technology evolves, staying updated on future trends will keep you competitive. So, whether you're fixing a dent or crafting a custom exhaust, remember: practice, persistence, and passion are your keys to success in automotive welding.